三、聚酯模塑料的制備
1.SMC的制備
(1)SMC的生產設備
SMC生產主體上分為兩部分:一部分是樹脂糊的制備設備,它包括投料、混合、輸送三個過程。一部分是制片設備,它包括上糊、粗紗切割、浸漬壓實和收卷。本部分主要介紹SMC制片設備。
一個完整的SMC機組,大體由機架、輸送系統、PE薄膜供給裝置、刮刀、玻璃纖維切割器、浸漬和壓實裝置、收卷裝置等7個主要部分和玻璃纖維紗架、樹脂糊的制備及喂入系統、靜電消除器等3個必備輔助系統組成。
SMC機組組成如下示意圖所示。SMC機組典型照片如圖所示,典型SMC機組參數如表所示。
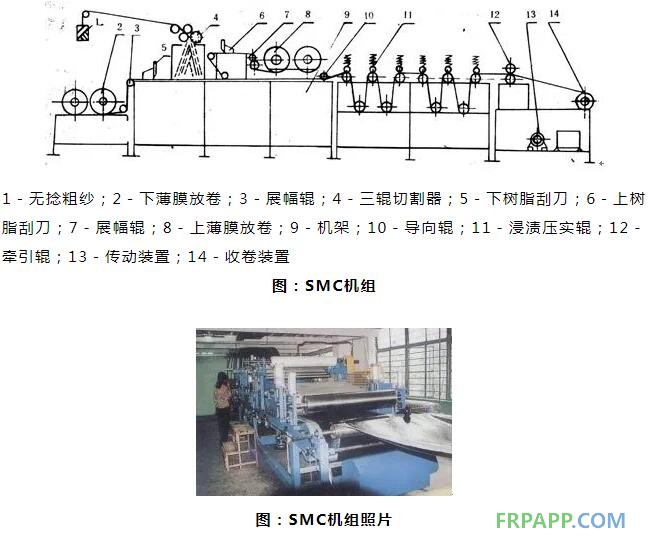
表:典型SMC機組參數
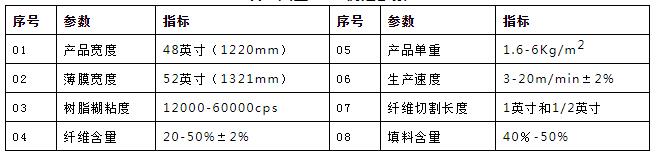
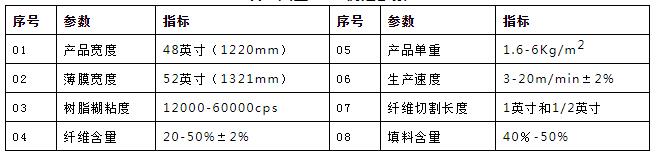
(a)機架
一般都用各種型鋼(如角鋼、槽鋼等)焊接或用螺栓連接而成,它的主要作用是安裝輸送系統和各種部件。為防止在各種靜載荷、動載荷下的變形,機架應有足夠的剛性,并且在新結構設計中,往往應在機架上留有備用空間。
(b)輸送系統
一般有兩種類型,一種是輸送帶,一種是直接用聚乙烯(PE)膜兼起輸送帶作用。輸送帶運動軌跡控制裝置,在機組設計時要特別注意。
(c)PE膜供給裝置
PE膜供給裝置應保證在生產過程中有充足的薄膜供應,確保薄膜在有可調張力的情況下,無皺褶地進入上糊區。在機組中一般設有兩套供膜裝置,而每套能同時安裝兩卷薄膜,以便在一卷薄膜用完后,另一卷備用薄膜能立即投入使用而不會引起生產過程的停頓。
(d)刮刀裝置
在機組上糊區,安有兩個刮刀裝置。其主要作用是隨著薄膜在刮刀及其底板間通過時,均勻地將可控數量的樹脂糊施加到PE膜上。刮刀應容易調節且調節精度要高,刮刀與底板間的間隙要均勻,誤差應在0.05mm以下。為防止樹脂糊中結塊或外部雜質進入刮糊區引起薄膜的扯裂,刮刀底板或刮刀可實現臨時性的瞬間下降。設計時,還應使刮刀刃部的半徑盡可能小。
(e)玻璃纖維切割
在許多較早設計的機組中,切割器單獨安裝在另一個機器上,當改用玻璃纖維氈時,設備不必做過大的改動就能生產。但是,目前由于價格和性能方面的原因,已很少使用氈作SMC的增強材料,因此切割器大多直接固定在主機架上。玻璃纖維由切割器切斷。切割器為三輥式結構,如圖43.178所示。連續玻璃纖維從紗架引出,經紗線橫動桿2進入壓輥5與橡膠包覆的支承輥3之間后,由于兩輥的牽引,纖維被導入轉動的支承輥與切割輥8之間,被切成短切玻璃纖維。
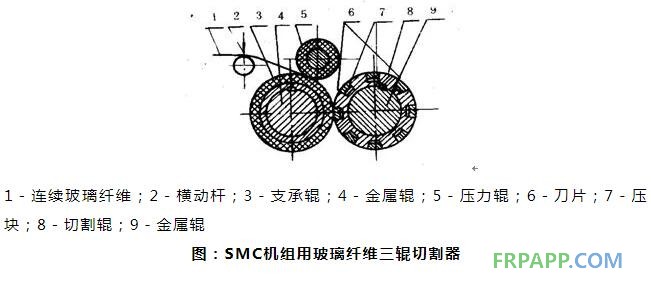
(f)浸漬與壓實裝置
浸漬與壓實裝置由一系列光輥和槽輥組成,在個別機組中還加有刺穿輥。它們的作用是實現SMC片材的復合、浸漬、脫泡和壓實,槽輥的使用可以強化浸漬,而且避免發生在浸漬壓力下樹脂糊外流現象。在浸漬壓實區,各種輥的壓力可采用氣體或液體加壓,該區尾部的壓實輥,還起到調節片材厚度的作用。在SMC機組中,浸漬、脫泡、壓實主要靠各種輥及片材自身所產生的彎曲、延伸、壓縮和揉捏等作用實現的。為使纖維被樹脂浸透、驅趕氣泡和使片材模塑料壓實成均勻的厚度,機組中有兩種浸漬壓實結構,即多輥筒的環槽壓輥式與輸送帶的彎曲雙帶式,如圖及圖所示。
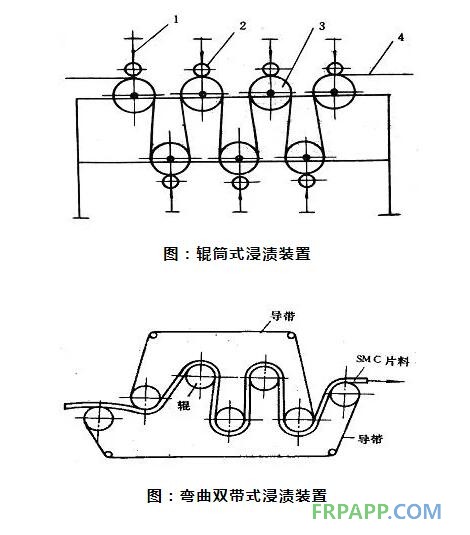
(g)收卷裝置
收卷裝置的作用,就是將經過浸漬的SMC收集成卷。對于試驗性機組或小批量生產機組,一般采用雙軸雙位轉臺式收卷裝置,這種裝置可在生產過程中實現換卷。
(2)SMC的生產工藝
SMC片材的制備主要由如下幾個部分組成:
(a)樹脂糊制備及上糊過程.
樹脂糊的制備方法有3種:
a)批混合法 此法是把增稠劑以外的各種材料按比例加入反應釜中,以一種糊狀混合物的形式使用。在上SMC機組前加入增稠劑。增稠劑加入后,通常在30分鐘內使用完。
b)批混合/連續混合法 該工藝的特點是用兩個混料釜系統混合。一個裝不飽和聚酯樹脂、低收縮添加劑、引發劑、脫模劑和填料,另外一個釜里裝載體樹脂、著色劑、增稠劑。生產時,用計量泵通過混合器進行混合。
c)連續混合法 配方中的所有液體或固體的計量、運輸、混合全部實現機械機械化和自動化。此系統裝置投資費用大,適合連續大批量生產。
(b)浸漬過程
浸漬過程的目的是使樹脂浸透纖維、驅趕氣泡、使片材壓緊。為此,SMC機組中排列了各種類型的輥(光輥、槽輥、穿刺輥及螺旋輥等)。當片材從這些輥的上部、下部及周圍經過時,因受到彎曲延伸作用而實現浸漬。
(c)增稠過程與存放過程
當SMC片材收卷完成后,一般要經過一定的增稠時間后才能使用。如SMC片材在室溫下存放,大約需要1~2周。在40℃稠化需要48小時或72小時。目前也有在SMC機組上增設增稠區域或采用一些新型的增稠劑,SMC制備成片材后即可進行壓制。
片材的儲存期與儲存狀態和條件有關。環境溫度對SMC片材的儲存期有明顯的影響。以英國的SCOTT BARD公司生產的片材為例,它在15℃以下的儲存期為3個月;在2~3℃的儲存期為6個月。片材的儲存期也與配方有關。如配方中加入阻聚劑,儲存期就會長一些。
(3)SMC的生產過程控制
如上所述,SMC是由多種組分經專門的設備復合而成。從原材料方面看,它既有有機材料又有無機材料;既有固體材料又有液體材料;既有粉體材料又有纖維材料,而且各組分復合在一起的時候開始,系統會產生各種各樣的物理和化學的變化。在其生產過程中,有很多因素,如材料因素、設備因素、人為因素等都會影響到生產的過程和最終產品的質量。因此,只有從整個生產系統包括從使用角度來考慮片狀模塑料的全面質量管理,才能得到一個質量良好、相當穩定的片狀模塑料產品。
一般而言,SMC制造的質量管理由二部分組成,即原材料進廠質量管理、SMC生產工藝過程管理。
(a)原材料的質量管理
SMC生產用原材料主要包括不飽和聚酯樹脂、低收縮添加劑、苯乙烯單體、填料、玻璃纖維、內脫模劑、引發劑、色漿、化學增稠劑等,需要控制的項目列于表。
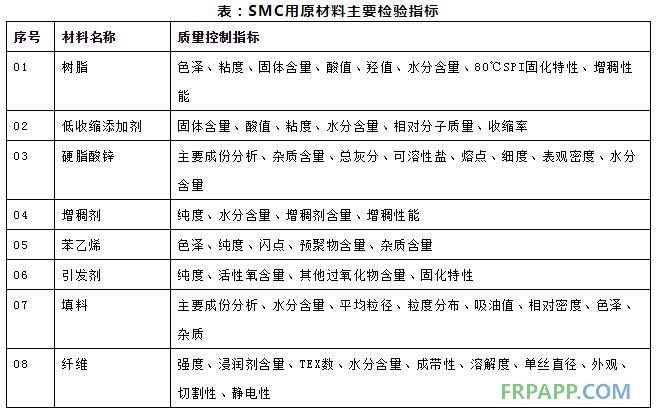
需要強調的是上表中列出的項目并不是需要逐項測試。在整個SMC片材生產過程中尤其需要注意嚴格控制體系的含水量,尤其是原材料體系的水分含量。
(b)SMC工藝質量管理
SMC生產過程包括如下步驟:投料、混合、樹脂糊的輸送與涂敷、 纖維輸送與切割、復合與浸漬、收卷與計量、熟化。后續按照SMC工藝控制和質量控制兩方面進行描述。
a)SMC工藝控制
在線的伽瑪射線測試裝置持續測量載體薄膜上的SMC/BMC樹脂糊的厚度,保持載體薄膜上的SMC/BMC樹脂糊的厚度一致(在寬度方向,SMC糊分布均勻一致,沒有偏差),保持玻纖分布均勻及穩定的玻纖含量( 2%);
通過裁剪SMC并稱重的方法在SMC寬度方向的不同位置處測量單位面積SMC的重量;在生產開始時,生產過程中間以及生產結束時分別測量單位面積SMC的重量(控制SMC厚度均勻的一種方法);
在更換樹脂及使用新的批次的填料時應測試樹脂糊的粘度和溫度;將SMC貯存在恒定和受控的環境中,即較高溫度的熟化室(如28℃)和較低溫度的貯存室(如18℃);為了控制SMC/BMC糊的粘度增長,生產中需將SMC/BMC樹脂糊樣品貯存在SMC/BMC熟化室,并按規定使用布氏粘度計測量SMC/BMC樹脂糊的增稠情況;在添加原料如樹脂、填料、助劑、氧化鎂糊時添加量要準確。
b)SMC質量測試
用放熱試驗設備測試SMC的反應性,如沒有反應性測試儀,通過熱電偶測量平板成型過程中的溫度隨時間的變化曲線;測量平板的收縮率;用塑化儀測試SMC的稠度(塑性程度),該方法非常適合于相同配方SMC的生產監控,如果生產中所用的纖維有變化,測試結果就會不同。
(4)SMC生產過程中常見問題及解決方法
表:列出了SMC片材生產過程中的常見問題、產生原因及解決方法。
表:SMC生產過程中常見問題及解決方法
表:SMC生產過程中常見問題及解決方法