1 引 言
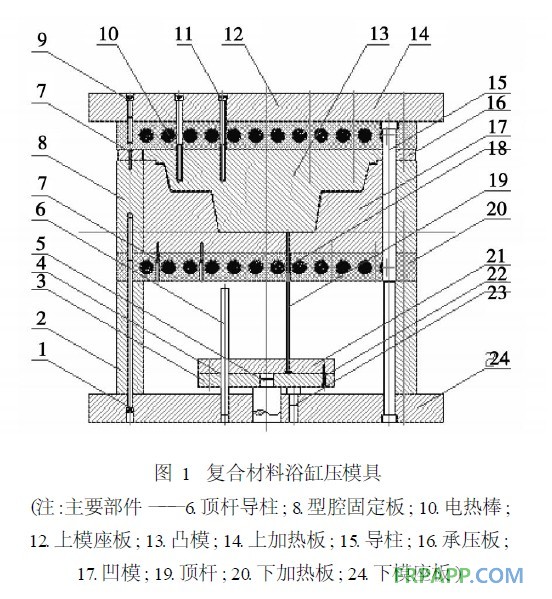
傳統的浴缸制造材料一般分為三大類:玻璃鋼、鋼和鑄鐵。玻璃鋼浴缸的表面硬度低,易劃傷,耐磨性差。鋼這種材料比較堅硬耐用,鋼制浴缸需要有陶瓷或搪瓷覆蓋表層。鑄鐵是十分耐磨的材料,但是鑄鐵浴缸的缺點是保溫性能差,熱水會很快變涼。而最新流行的SMC (片狀模塑料)復合材料浴缸則能避免上述缺陷。
2 復合材料SMC (片狀模塑料)
SMC ( SheetMolding Compound)即片狀模塑料。六十年代中期,西德(Bayer公司)實現了SMC工業化生產 , 1970年開始在全世界迅速發展。SMC的發展已經成為近30年來FRP (學稱纖維增強塑料,國內習慣上稱之為玻璃鋼。它是以合成樹脂為基體材料,以玻璃纖維及其制品為增強材料組成的復合材料)最顯著的成就之一。
SMC主要原料由GF (專用紗) 、UP (不飽和樹脂) 、低收縮添加劑、MD (填料)及各種助劑組成,是樹脂基復合材料的一種。并在兩面用聚乙烯或聚丙烯薄膜包覆起來形成的片狀模壓材料。使用時,只需將兩面的薄膜撕去,按制品的尺寸裁切、疊層、放入模具中加溫、加壓,即可得到所需的制品。SMC材料具有優越的電絕緣性能、機械性能、熱穩定性、耐化學防腐性,質輕及工程設計容易、靈活等優點 ,其機械性能可以與部分金屬材料相媲美,其制造的產品具有良好的剛性、耐變形、使用溫度范圍大的優點。
3 復合材料浴缸模壓模具設計
設計的圓形按摩式浴缸(圖1 ) 外部尺寸為:1620 ×1620 ×500 (mm) ,厚度為5mm,成型工藝采用模壓成型的工藝方式,浴缸模壓材料選用熱固型SMC (片狀模塑料) 。復合材料浴缸模壓模具(圖1)的設計主要由以下幾個部分: (1) 成型部分:包括凸、凹模; (2) 加熱部分:包括加熱板; ( 3) 支承部分: 包括墊板、固定板、承壓板; (4) 頂出機構及導向裝置:包括導柱、頂桿導柱、導套、頂桿、拉桿; ( 5) 連接件:包括各部分螺釘等。改進和優化了傳統的壓模結構。用三維軟件建模如圖2。
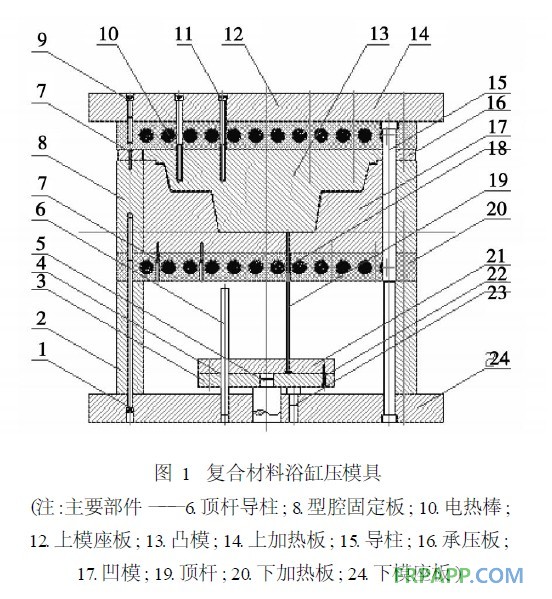
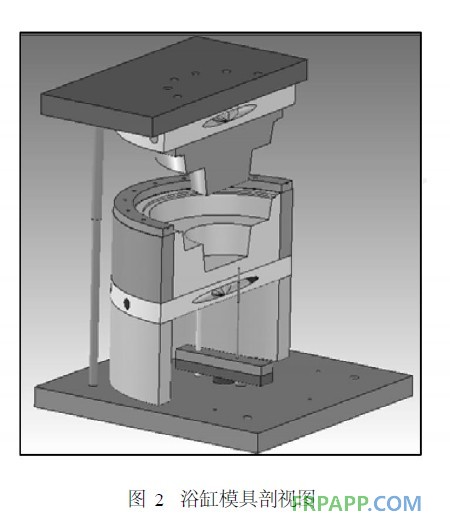
適合于加工SMC模壓模具的材料有球墨鑄鐵、鍛鋼、鑄鋼、預硬化鋼、正火鋼等幾種。在選擇模具的材料時,首先要考慮材料可以加工的尺寸, 然后要根據產品的具體情況,對模具材料的強度、堅韌性、硬度、耐磨性、尺寸穩定性、可加工性、可焊接性、可拋光性、材料價格等作出綜合選擇 。
4 模壓成型工藝分析
模壓成型工藝的基本過程是將一定量的經過一定預處理的模壓料放入預熱的壓模內,施加較高的壓力使模壓料充滿模腔。在預定的溫度條件下,模壓料在模腔內逐漸固化,然后將制品從壓模內取出,再進行必要的輔助加工即得到最終制品。片狀模塑料的模壓成型過程是首先將合乎要求的片狀模塑料剪裁成所需的形狀,揭去兩面的保護薄膜,按一定的要求疊合,然后放置在模具的適當位置上,按規定的工藝參數加溫加壓成型 。
復合材料模壓制品的壓制工藝(圖3)壓料裝模后在固化劑存在或加熱的條件下在模腔內固化成制品的過程。成型溫度和成型壓力共同影響著SMC制品的質量,要在綜合考慮各種影響因素的情況下,確定出最佳的成型溫度、成型壓力及保壓時間 。
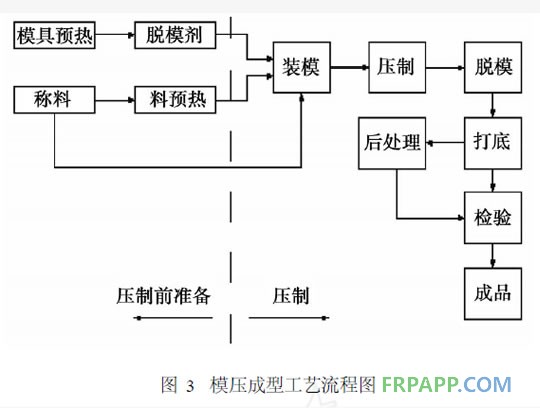
模壓成型工藝具有如下優點 :
(1)由于沒有澆注系統,故原料的損失小(通常為制品質量的2% —5% ) 。
(2)由于模腔內的塑料所受的壓力較均勻,在壓力作用下所產生的流動距離較短形變量較小,且流動是多方向的。因此,制品的內應力很低,從而制品的翹曲變形也很小,機械性能較穩定。
(3)特別適于成型不得翹曲的薄壁制品;可成型較大型平板狀,盆狀的制品。
模壓成型也存在如下缺點:
(1)對存在凹陷、側面斜度或小孔等的復雜制品,可能不適合采用模壓方法成型。因為這要求模具的結構較復雜,還可能發生熔體在較高壓力作用下流動時使模具銷軸、側芯等彎曲,甚至折斷的現象。對壁厚大于9mm 的制品,尤其是厚壁小面積的制品。
(2)由于一般模壓料熔體的粘度很高,要使之完全充模可能存在問題。為了保證熔體能完全充??赡鼙仨毎涯毫现糜谀G粌鹊囊粋€最佳位置,有時要把模壓料預制成特殊形狀的料坯。這對模具沒有提供一種把模壓料限制在某一特定位置的措施時,顯得特別重要。
(3)固化階段結束并開模取出制品時,制品的剛度不同是要考慮的一個重要問題。例如,三聚氰胺甲醛制品的硬度、剛度很高,酚醛制品較柔軟,未增強聚酯制品的剛性則相當差。這樣,一套模具模壓成型無斜度或甚至有適度凹陷的酚醛制品時,工作的可能很好。但同樣的模具對三聚氰胺甲醛而言,開模要求高得多的壓力,可能會使制品凹陷處龜裂,而模壓聚酯制品時,模具需要設置較多的頂桿。
5 結 語
拋開了傳統的塑料制品的生產制造工藝,根據復合材料SMC的材料性能,選擇模壓壓制成型的工藝方式,在傳統的典型的壓模結構設計的基礎上進行了改進和優化,將材料的優良性能和模壓工藝的優點完美的結合起來,達到了優化、簡便、適用和經濟的理想效果。