所以,要制備高品質的SMC/BMC,首先要根據成品的性能要求確定玻璃纖維的含量,根據玻璃纖維的含量和增稠特性,正確的選擇原材料及配方,選擇正確恰當的粘度范圍和增稠速度,同時通過對樹脂糊粘度的影響因素中外因的合理控制,使樹脂糊達到理想的增稠速率,良好地浸漬玻纖。
3 二異氰酸酯化合物增稠
氧化鎂增稠劑價格低,但增稠速度慢,其粒度、分散性、活性等因素對樹脂的增稠性能也有較大影響,從而導至增稠效果不穩定。使用二異氰酸酯化合物進行增稠也稱ITP(Interpenetrating Thickening Process)技術,它以二異氰酸酯作為增稠劑,利用二異氰酸酯化合物與不飽和聚酯反應生成一種交替分散的高分子網狀片段,這種網狀片段是由兩種聚合經交聯與互穿所形成的網絡組成的一種精密聚合物。這種技術可以更快、更有效地控制粘度,而且模壓制品收縮率低、沖擊強度高,容易得到強韌性材料。采用這種技術制成的具有獨特機電性能的SMC/BMC片材,其貯存穩定性長達一年,且制品長期暴露在高濕環境下電氣性能仍很高。
甲苯二異氰酸酯(TDI)在貯存過程中,尤其在常溫下貯存,易發生自聚形成二聚體而改變其性能,為防止其自聚需在0℃下低溫貯存、運輸,這不僅不方便,還增大貯運費用。當采用異氰酸酯單體對不飽和聚酯樹脂增稠時,-NCO基團的反應活性很強,增稠劑的加入速度不能太快否則在攪拌不均勻的情況下,樹脂可能出現凝膠現象,同時異氰酸酯單體初期增稠過快,各種增稠劑的增稠曲線見圖5。
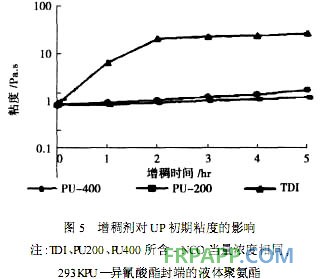
當采用PU200和PU400對不飽和樹脂(UP)增稠時,在初始的4hr中粘度增長平緩;當采用TDI單體對UP增稠時,增稠過程中初期粘度增長較快,
2小時后樹脂粘度達21.4Pa·s,這一粘度會給玻璃纖維的浸漬帶來困難。產生這種變化的原因可能是TDI的兩個-NCO基中,對位的活性比鄰位的活性高8~10倍。當采用TDI對不飽和聚酯樹脂增稠時,對位-NCO基易與樹脂中羥基反應,因此體系的粘度增加較快。而在PU200或PU400中,對位的-NCO基已反應,剩下的是活性較弱的鄰位的-NCO基。因此采用異氰酸酯預聚體對不飽和聚酯樹脂增稠速率均勻,而且不易凝膠,可見采用PU400或PU200等異氰酸酯預聚物對UP增稠是比較適宜的。 隨著增稠劑的增加,增稠效果變好(見圖6)。這可以歸因于隨著增稠劑的增加,體系中-NCO基濃度增大,反應速度加快。但當Wpu達到15%時,樹脂的初期粘度增長過快,2hr后粘度達到24.6Pa·s,因此增稠后的樹脂糊在2hr之后已無法正常浸漬玻璃纖維。可見采用PU400對不飽和聚酯樹脂增稠時,增稠劑的質量百分用量要限制在10%以內,否則樹脂無法正常浸漬玻璃纖維。 ![]() 在相的同Wpu下,增稠速度隨著增稠劑分子量的增大而下降(如圖7所示)。這是因為,增稠劑分子量越大,其分子數越少,體系中-NCO基濃度越低,因而增稠速度越慢。 ![]() |
在273K(0℃)下,盡管樹脂增稠較為緩慢,但在四天內仍可完成增稠。在293K(即室溫20℃)下,初期增稠較慢,一天后基本完成增稠。在323K(50℃)下增稠速度很快,在8hr內即可完成增稠。可見,異氰酸酸對UP樹脂的增稠溫度存在一定的依賴性,但這種依賴性并不影響異氰酸酯對UP樹脂的增稠,無論在273K,還是在293K、323K下,增稠的過程都能在四天內完成。
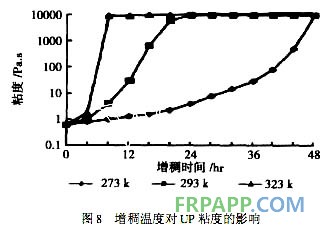
SMC/BMC片材熟化后,在高溫固化之前應具有優異的貯存穩定性,即粘度不應有顯著的增加,物料在模壓時應保持良好的流動性。熱固性注射塑料螺線流動實驗是測量這種流動性的一種方法,因此,可根據測量物料在規定條件下通過澆口進入螺線模腔中的流動長度來評價片材的貯存穩定性。圖9為分別使用MgO和異氰酸酯預聚體增稠的SMC/BMC片材的螺線長度隨貯存時間的變化(貯存溫度:10℃)。
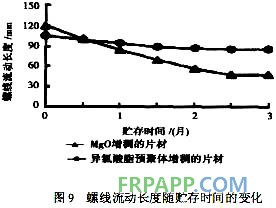
圖9表明無論采用MgO增稠體系還是異氰酸酯增稠體系,SMC/BMC片材的螺線流動長度都隨貯存時間的延長而縮短。貯存三個月后,由異氰酸酯增稠體系制備的片材的螺線長度變化較小,僅從105mm降到86mm,而MgO增稠體系的片材的螺線長度從120mm降到48mm。
4 結果與討論
MgO增稠的樹脂體系貯存穩定性較差,而異氰酸酯增稠的樹脂體系貯存穩定性相對要好,其片材的加工流動性很好。
產生這種現象的原因可能是MgO增稠的樹脂在增稠結束后和貯存過程中,由于金屬氧化物的存在,發生了進一步的絡合反應和催化不飽和雙鍵的聚合反應,導致物料在高溫模壓時流動性變差。而異氰酸酯增稠的樹脂在增稠過程中已經稠化得很徹底,不再催化進一步的絡合反應或不飽和雙鍵的聚合反應,因而異氰酸酯增稠的樹脂片材具有良好的貯存穩定性。